- Popular Post
-
Posts
1628 -
Joined
-
Last visited
-
Days Won
8
Content Type
Profiles
Forums
Events
Gallery
Store
supertorial
Classifieds
Posts posted by rodeo bill
-
-
12 hours ago, AlientoyWorkmachine said:
do you ever plan to make more 900's - other dyes or even just unborn? The one I've got has a long life ahead of it but I do love the pattern of that jacket.
yes
more soon!
5 -
EDIT! @srudy and @AlientoyWorkmachine I'm so sorry- I just took a closer look and you're both completely right- this is indeed the Old North Cross Weave Indian Black jacket.
It's a really nice one, and as Alientoy says this photo looks a little darker than the garment in real life. At least I can say that it too comes up slimmer than the woad standard denim version, so should fit you ok Srudy. This fabric was particularly hard to sew into the tight angles of this jacket, so I don't expect to repeat it, and there were only 12 pieces made- great find!I'm so sorry for the mixup, I should have looked more closely before posting. As I said,
2 -
On 10/15/2021 at 4:58 PM, srudy said:
Found this 900 beauty on Grailed and picked it up for a steal. I’m hoping even though it’s a 4, it’ll still look cool and not too oversized, although that might not be a bad thing either.
On 10/15/2021 at 7:03 PM, JDelage said:Is that a black version?
On 10/15/2021 at 7:49 PM, AlientoyWorkmachine said:not my jacket but looks like the same one I own which is the Old North one - it's the 19 oz crossweave w indian black overdye. It also looks like the image is a bit underexposed as it's not really that dark, or at least mine's not.
On 10/15/2021 at 8:40 PM, srudy said:Yep! The Old North one!
Nice find @srudy! It is a black one, but not the Old North special I don't think (which was Cross Weave denim, Indian Black, and indeed not this dark). I'm pretty sure from the photo that this is from 2011 and is regular selvage denim, dyed with logwood. It came with a natural black sheep's wool liner, which doesn't seem to be in this photo. I don't have any very good photos of this one, but here are a couple that I dug out:
This one was dyed hot so shrank quite a bit more than the woad version- with luck the sizing should be ok. Let us know when you receive it!
7 -
38 minutes ago, MJF9 said:
Crazy marbling indeed… have you changed denim William?
nope, exactly the same as always- developed in 2009 and remade every couple of years since then!
3 -
31 minutes ago, AlientoyWorkmachine said:
@rodeo bill that is a great looking cut. That marbling is wild!
thank you, and yes! this denim marbles really beautifully- it's a very very dark indigo to start with, almost looks black, with 25 dips in indigo, and it marbles really nicely, especially if you wash a few times from raw without too much wear in between.
1 -
On 10/11/2021 at 1:28 PM, redragon said:
^
Still waiting for you to remake type 131, the baggy fit is definitely not for everyone but its one of the comfiest cut I had ever worn.
I get asked about Type 131 every now and again- it's developed something of a (to put it very mildly) niche, following. I think I made 10 pairs for Burg & Schild in Berlin, in 2011. The only problem is I never made a pattern for them, they were just a freehand addition to the 130 pattern (if I remember correctly), drawn directly onto the fabric before it was cut. Someday I'll look through old emails (it doesn't help that I've switched my email service since then) and see if I can work out exactly what shape they were.
On 10/11/2021 at 9:02 PM, sven said:I stumbled across these pictures of Douglas from Second Sunrise wearing the 136
Thanks for the link Sven- Douglas really gets beautiful wear into his jeans, I hadn't seen these since they were new!
@JDelage and @Broark many thanks for this. I was planning to put up some photos here, anyway. So for starters, here are my own 125s after a couple of months and several washes:
There's a nice amount of leg twist, but I'm also really taken with the twist in the top block- you see it more clearly in this worn photo:
The measurements for 125 aren't dramatically different to 130 or 132- the waist is around 1/2" higher in front and 3/4" higher in the back, and the hem is somewhere between 130 and 132 with a similar thigh and straighter leg than 130, a bit narrower than 132. Most of the difference is in the shape of the top, which is cut straighter than 130 or 132. If you imagine the fabric was striped, you'd see the stripes converge on the fly more on 130 or 132, while they'd be more parallel across the fly on 125, if that makes sense? It's not too dramatic of a cut, and I'm really enjoying wearing mine. These are a size 4, which is my size in all the Tender jeans I wear, and I'm around a 35" measured waist.
16 -
14 hours ago, sven said:
So impressed by your work @rodeo bill.
I only recently found out about Tender, but the craftsmanship and the originality of the designs is so impressive that is has become my favorite brand. Can’t wait to own a piece and love it for a long time.
Torn between the 132 and the 136 cuts. How do they compare?
Thank you so much for this, Sven! I'm really pleased you like the look of my things.
132 was the first Tender jeans fit, and is relatively wide and pretty straight, but depending on how you size it doesn't wear as wide as you might expect, more of a workwear sort of shape. 136s are similar to 132s at the top (fairly roomy without being baggy, mid/high rise) but are considerably wider through the leg to the hem- they're definitely a wide legged style, and as wide as I'd go before they start to look silly- they're still very wearable.
I generally prefer looser jeans (personally), so even type 129 'slim' jeans aren't skinny by many standards. On that basis 132 is the standard Tender model and 136 is the wide leg. They both have a very nice vintage feeling, I think, without specifically referencing particular periods or brands.
That was a bit of a ramble! but I hope it makes sense. Please feel free to email me if you'd like full measurements for any specific sizes.
1 -
-
18 hours ago, AlientoyWorkmachine said:
Just a quick update on my 129 Woads after the second wash. About 2 years old probably 7-8 months of wear.
Looking good! thank you, and I'm really pleased you're enjoying the cut- slim but doesn't feel that way was exactly what I was going for! I'm wearing a pair of 129s at the moment, too, from Unborn:
These have been a useful learning experience for me. I always recommend washing jeans fairly regularly, and not wearing them too tight, but this is the first time I've really tested that advice personally. These are size 4, and fit nicely when they were raw. I worn them about 6 months on and off without a wash, them washed them and they got too tight for me. I've since lost a bit of weight and they've stretched out a bit too, to now fit really nicely, relatively slim. But I'm seeing the cotton thread wear through much more quickly than I've ever had with my jeans that I've washed more frequently. I'll do some small repairs on the parts that are going, and I'm enjoying the relatively contrasty fading that I've not had for ages, but I stick by my recommendation to err on the looser side and to wash reasonably frequently!
19 -
On 7/27/2021 at 1:07 AM, heyson said:
Hey @julian-wolf thank you. For me it is a hard fix ha!
I was supposed to post some pictures and thoughts of them over a year ago, I think you had asked about them then. Sorry about that things got away from me.
I love them. They are aging very subtly which is great. I’m thinking about ordering a size up as I’d like them to fit a bit looser. I will put up some detail shots.
Sorry to see this. Julian's right that it's fixable- a good local tailor should be able to put a patch behind the rip and then sew over it from the outside.
I have a soft spot for Whooper, and I've really enjoyed my pairs. I've not got much stock left, though, and I have all that there is. Please just let me know if you have any questions.
0 -
On 6/21/2021 at 7:45 AM, beautiful_FrEaK said:
If you ever wanted to visit an Evisu store but were never able to...now you can:
https://my.matterport.com/show/?m=9G8v5WiwT7C
did anyone else spot Mr Yamane having a whisky on the top floor?!
6 -
24 minutes ago, julian-wolf said:
receiving the elephant mug wrapped in an extra swath of it seems to have been very timely (& the mug itself exceeds expectations, too!)
Thanks! Yup I thought you'd like to see the fabric in person :-)
1 -
^this looks fantastic on you! thanks for the photo!
1 -
8 hours ago, julian-wolf said:
It’s not quite the same, since here you’ve still woven the fabric as a warp-facing twill, such that the jeans are truly cut inside out (face in) rather than just weft-side out (but still face out)—but it’s an interesting comparison to make all the same.
Thanks very much for your insight! I'm not sure if I was quite clear- the fabric is cut face-out, not inside-out, it's just cut across the piece so that the indigo weft becomes the vertical on the garment (as it would be if it was a warp cut lengthways). The ecru warp was pushed back in the weave to let more blue show on the front (which is why the inside of the jeans show a bit more white than with normal denim), but it's still an indigo face/ecru back cloth. Sorry if I'm being pedantic! I love this:
8 hours ago, julian-wolf said:there’s so much more to it than just the sort of dye and the number of dips!
1 -
- Popular Post
- Popular Post
-
Great outfit @AlientoyWorkmachine, and thank you or noticing the photo shoots! I don't do much photography myself these days, but I've always loved it as a medium, and I have a really good relationship with the photographer who's shot the past 7 years or so's worth of seasons. We always try to do something interesting with the equipment and film, as well as locations and compositions. It's one of my favourite parts of the process :-)
Speaking of Cross Weave denim, over the past few weeks I've been getting some very-long-delayed 19oz Cross Weave jeans in stock. These were cut out in 2018, but only just got made- the cut fabric has been sitting at the factory for nearly three years... I think they're worth the wait, though, they've come out really nicely. Here are some closeups of a pair of walnut dyed 132s:
The Cross Weave fabric is a pretty simple idea, but I've not seen it done before. Normal denim is an indigo warp (up/down) and a white weft (side/side), and normal jeans are cut along the length of the fabric (which is why eg the selvage of the fabric runs up the leg). With Cross Weave denim the warp is ecru (a very substantial canvas weight unbleached and un-shrunk cotton) and the weft is the Japanese-spun and rope-dyed indigo cotton that's used as the warp in standard Tender denim. Looking at the fabric on a roll, the twill is woven at quite an oblique angle, and it's a left hand twill. The jeans, however, are cut across the fabric, ie at 90 degrees from normal, so the twill becomes much more normal looking, and it's a right hand twill. I wasn't sure if this would work as a normal right hand twill, but it does! This isn't the most convincing photo, but you can see that there's a pretty definite clockwise twist (especially noticeable on the left leg in this photo), which means the rotated-left-hand-twill is indeed twisting like a normal right hand twill:
These jeans are cut without a side seam, but other than that are the standard jeans patterns and spec.
13 -
- Popular Post
- Popular Post
Spring is here! At least in the UK, more or less. I'm starting to get some new Weaver's Stock shirts and jackets in, cut from some really special deadstock Northern-Irish-woven linens and linen/cottons. Here are the season photoshoot images, shot on deadstock infrared film in a strong breeze!:
This collection was put together at the beginning of last summer, when everything felt extremely uncertain. My mainline sewing factory was shut down completely, as was my main weaving factory, and I didn't want to commit to making too many new styles for stockists in case I wasn't able to deliver. Hence this Weaver's Stock collection is relatively modest, but I think really makes the most of some truly lovely fabrics. It's all ends-of-rolls, which has caused production headaches of its own, but I'll be getting a few more pieces in in various patterns over the coming weeks.
Alongside that, very thankfully all the people that I work with are safe and well, and more or less returned to normal working. This has given me a bit of mainline production space to catch up on restocks, including jeans (mostly now sold, I'm happy and sorry to say), and a big restock of mainline shirts, mixing previous seasons' styles with different seasons' fabrics and dyes. All going up on the Stores over the next few weeks, and I'll try to get some pictures up here, too!
26 -
On 2/22/2021 at 10:15 PM, maharu said:
Unborn molleton 130 just in. Wow! Very hard to photo the brushed, a bit fluffy, fabric. Definitely something special!
Thank you! Sorry to be so slow with this, and I recently put these pictures on Instagram, but in case anyone's interested here is a lovely pair of denim molleton 129s in for some repairs. I'd not seen a pair of these worn in- the softness, especially on the inside, is really remarkable compared to the regular denim. I'd say the wear and fades are a bit softer, too, which makes sense as the fabric isn't as crisp to start with:
15 -
I just received some photos from a great friend of the brand, and a long-time customer with some photos of his 10oz Cross Weave denim jeans. The fabric is woven in England with an ecru warp and an indigo weft (the same Japanese indigo yarn as used for the standard denim warp). I don't have a pair of these myself and I've not seen a pair worn in, although I've had good reports from a couple of customers. It's quite a soft fabric, but these have faded in really beautifully I think:
14 -
On 1/17/2021 at 4:42 PM, Double 0 Soul said:I was listening to some podcast last year... They were discussing the population boom in SF (800 peeps in 1849 to 20,000 in 1850) making food the most expensive commodity (a decent breakfast for 2 was the equivalent of $1200 today) by the 1860's enterprising folks were trying what'evs to source enough eggs to feed the hungry gold-rushing-loons, 'eggers' would go out to the Farallon Islands wearing specially made 'egging-shirts' with massive egg pockets for collecting the eggs of sea birds.Has ever such a shirt turned up? it would make an insane repro.
https://www.knau.org/post/gold-hungry-forty-niners-also-plundered-something-else-eggs
get to it people!
11 -
4 hours ago, julian-wolf said:
Funny—I remember looking at the Janus jackets when they first came out, but this is the first time I’m noticing how high up the sides the slits go
What’s that like when wearing it? Almost seems more like a poncho with sleeves & pockets
The idea with this one was to do inside pockets, without using jets or welts (like a suit jacket), or a pocket bag- one of my self-imposed rules with Tender has been that pocket construction must never be hidden. The 456 Janus Shirt has a double set of patch pockets on the outside- the upper pockets are open from above like conventional chest pockets, and the lower sections are hand-warmers. As with the 430 Butterfly shirt the pockets are moved to the centre, and sewn into an outward-facing placket, to avoid two sewing lines where one will do. Janus (two-faced) jackets, like this one, are the same garment turned inside out, so now the placket faces in, with the pockets on the inside. This gives you two inner breast pockets, reachable when the front of the jacket is open, but it would make the side pockets unusable without some sort of opening. Opening up the side seams to above the pocket height gives you access to the inner hand-warmer pockets, and also to jeans/trousers pockets, like with access slits in overalls.
Here are some photos from the season's shoot (the final images were hand-tinted, these are some extras in the original black and white):
this is the same fabric as @zverhope has for sale- thanks for the pics! I have a couple of different option in stock, too.
12 -
On 1/8/2021 at 5:42 PM, satchelbmoore said:
These are preeeetty cool
Thanks! Yes I'm really happy with how they came out. The corduroy is deadstock from a mill that used to weave in the UK but moved their production overseas years ago- they just had a few bits left of old British-woven cloth. It's a lovely soft cord and took washing really well. I particularly like how the wool flannel liner shrinks slightly more than the cord, so it pulls the edges in just a fraction, giving them a really nice 3D rolled edge. The body and pockets are lined with Welsh wool flannel, and the sleeves are lined with English cotton mattress ticking, so they're easier to pull on and off over other garments.
Here's the tan version, size 3, over a type 450 high back shirt and 136s:
15 -
- Popular Post
- Popular Post
following on from the Ten Years jacket and jeans, the photoshoot for the season also reproduced images from the first season, wearing the exact same garments after a decade of wear:
I'm not sure whether I've changed for the better, but the denim's worn in really nicely, and it's good to feel that designs from ten years ago are still something I'm happy to wear and produce.
32 -
^thanks for this. Not right now, but good to know you're interested- I really like this style, too, and it'd be good to repeat it some time.
Here are some factory photos of the 10th Anniversary jacket blanket lining fabric being finished. It's woven in Wales from Irish-spun donegal yarn, which is quite heavy and coarse as it comes off the loom, but this is where things get interesting. First it gets a wash, then to dry the fabric it goes through this:
this contraption moves the fabric very slowly, under tension, between very hot water pipes, the fabric goes in damp, so the room feels like a steam room. Here's a closeup of the hot pipes:
by the time it comes off the end of the rollers, the fabric is warm and dry, and has shrunk quite significantly, it looks like this:
the red loose threads hanging off the sides are the slip-yarns from the red stripes. You can see that they're a bit felted, from the hot process. Now the fabric get joined onto the end of whatever cloth was last in the raising machine:
this involves using a hand-cranked vertical wheeled sewing machine (similar to the equipment that's used to seal heavy-duty paper bags), to sew the end of the new fabric onto the end of the old fabric:
now the new fabric is attached, it can be fed into the raiser:
this is a big set of rollers covered in wire spikes, that revolve in opposite directions, acting in combination like a huge drum:
Once the machine's up and running, the whole length of fabric goes through:
here it is after one pass through the rollers:
the texture's starting together a bit fuzzier.
At this point, the whole length of fabric has gone through once, and the end of the fabric's coming up to the rollers. Now, the old bit of cloth that was sewn on at the start gets cut off, and the two ends of my fabric are sewn together:
now, like joining two ends of pasta to run it through a pasta machine, the fabric is a continuous loop and can be run back through the rollers. There's a bit of straightening up to do when the join gets onto the drum:
but once it's set, the machine runs continuously until the fabric has had three full raising passes, and is extremely fluffy on one side. At this point you could turn the cloth over and repeat the process on the reverse, but I like the contrast of the raised side versus the un-raised, and it also avoids weakening the yarn any more than necessary (if you passed the fabric through rollers too much, it would start to fall apart). Here's the cloth coming off a third pass:
now it's just a matter of opening the loop, by cutting the machine stitches:
then the finished cloth comes off the folder head of the machine, into a neat pile ready to be boarded and taken away to be sewn:
17
The Evolution of Jeans: Pictures, Scones and Tea
in superdenim
Posted
Just seen this, appreciate it's from ages ago! Please le me know if you'd like a replacement button pin- I can send you one out with pleasure. Either DM here or email.
Sorry to junk up the thread. As penance, here are the first prototype pair of Tender 125s. washed loads (maybe 10 times) over the last couple of months: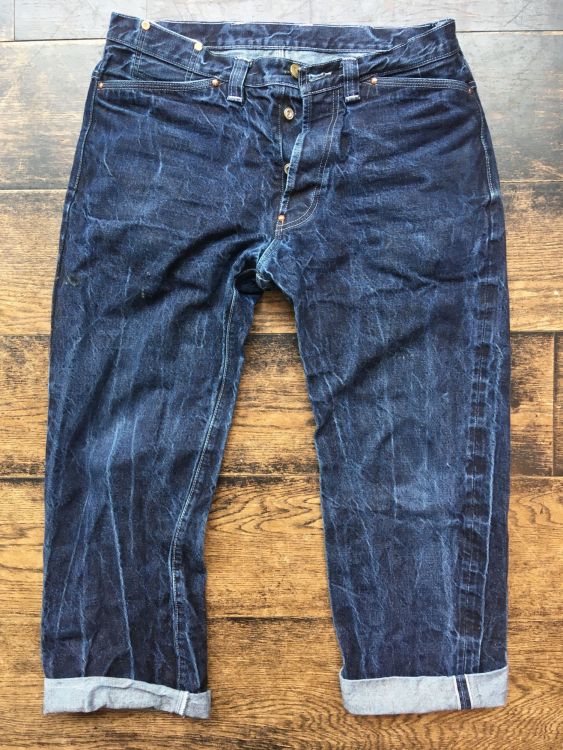