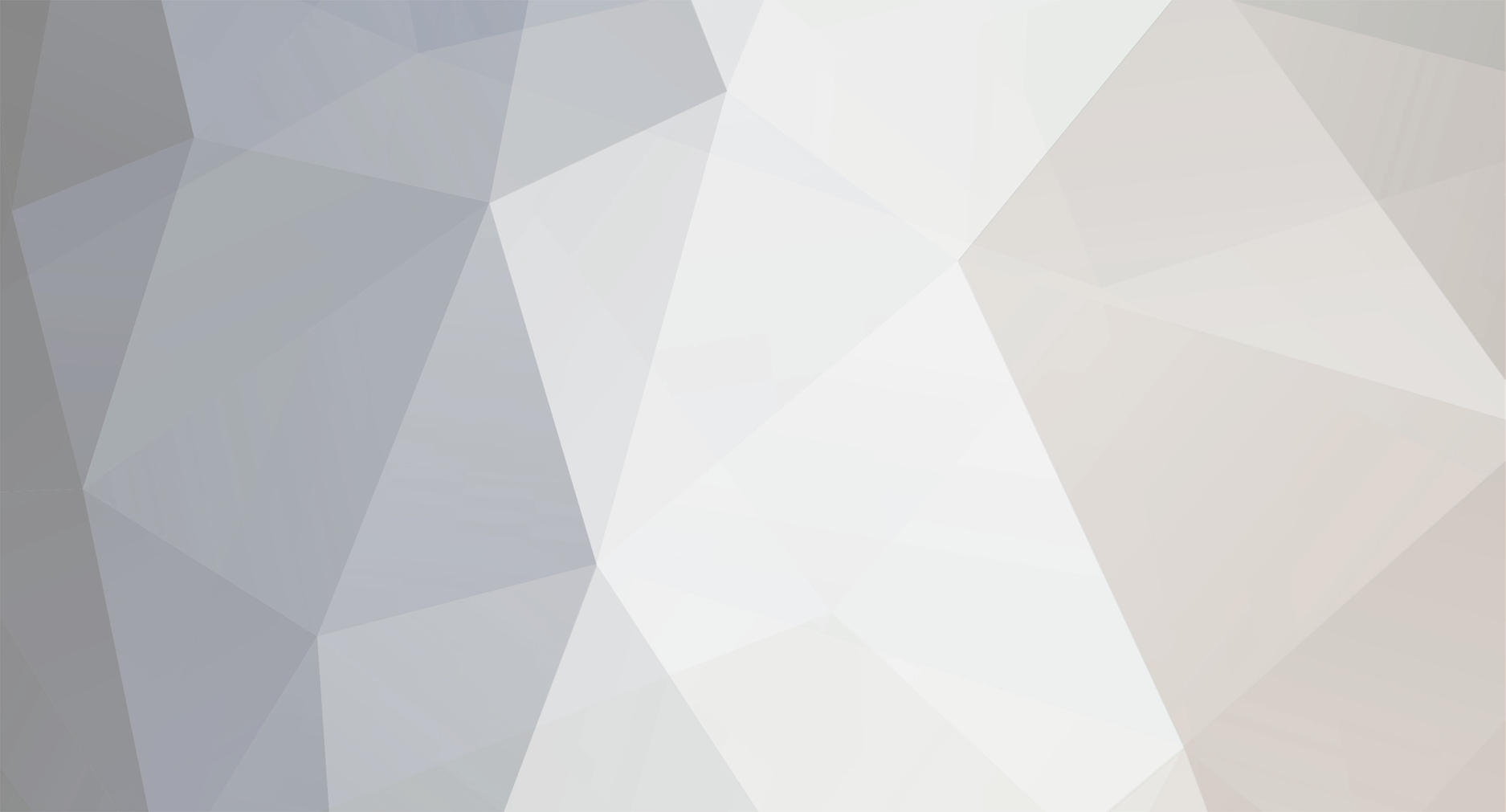
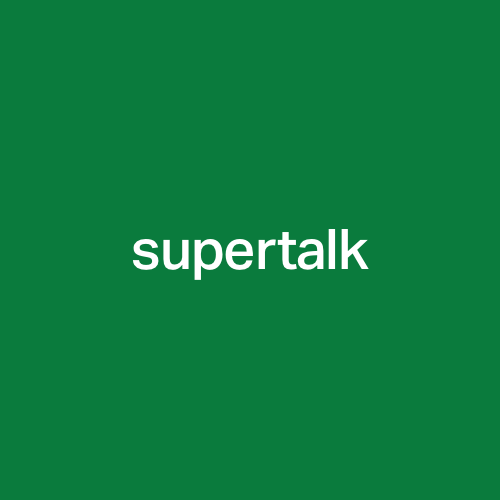
Lars
-
Posts
245 -
Joined
-
Last visited
Content Type
Profiles
Forums
Events
Gallery
Store
supertorial
Classifieds
Posts posted by Lars
-
-
Candyman, Candyman, Candyma....Quote:Quote: This technique can be repeated up to three times with raw denimDare I ask, what happens if you do it more than three times?
--- Original message by sonick on Mar 3, 2006 04:13 PM
0 -
Aha! I thought he was in cahoots with the seller somehow. Kids these days with their fancy proxy bids and cellphones..
0 -
I watched the bid history on those, and one bidder overbid himself 19 times during like 8 minutes, pushing the price from $1,350 to $3,480 is that really allowed?
0 -
What kind of ink is used for printing on leather patches? Can those be printed using normal screenprinting material? Any links are also appreciated.
What about rivets? I have found normal flat head rivets, but I want the kind of rivets that Levi's use. Where?
What about buttons? I have found normal flat buttons, but I want the donut hole kind. Where?
Again, links are greatly appreciated.
0 -
That's like saying shoes has always been popular. What I mean is that runners have come more into focus than they were a few years ago with the "street crowd".Quote:Quote: I hope this jogging shoe (Air max's New Balance..) fad dies out.Its hardly a fad, runners and bball shoes have been popular since before many of us were alive, and I supect will still be popular after we are all dead, and rightly so.
Edited by Ki_Adi_Monkey on Feb 14, 2006 at 01:10 PM
--- Original message by Ki_Adi_Monkey on Feb 14, 2006 01:09 PM
0 -
I hope this jogging shoe (Air max's New Balance..) fad dies out. It's only like 1 in 50 people that look good in them. The other 49 look like floor ball coaches..
Anyway, my money's on vans.
0 -
What does Switzerland have to do with anything?Quote:I used to chew because i'm fucking sweet, not because people in switzerland do. i hope nobody would start a lame habit like that so their jeans would look 'cool'. i think it looks trashy.
--- Original message by obsessis on Feb 14, 2006 04:45 AM
0 -
Photo quality = color separation + halftones.
All over prints are usually sublimation prints.
0 -
I ordered 1000 tags (the minimum at the place I got them) for about $150 and I just sew them onto the end of the sleev of the tee/sweat/hood. It's ghetto, but if you are doing runs of 25-50 shirts (mixed sizes) in each design you probably don't have the money to get custom necktags for your tees. If you do have the money, most screenprinters should be able to hook you up.
0 -
...yes?
0 -
Bah, plastisol isn't toxic
I've never been quite happy with waterbased inks.. they fade too much for my liking.
0 -
I never understood the appeal with supreme... still don't.
0 -
Looks nice. You have to figure out a way to get rid of that huge blood stain in your carpet though.
0 -
Stuff you need:
squeegee
photoemolusion
Some screenprinting ink
A screen.
A strong uv light
Oven (unless you go with some ink that just dries)
1. Coat the screen on both sides with photoemolusion. Put it in a light proof place over night.
2. Print out your design onto plastic film.
3. Put the film on the back side of your screen and expose it with the uv light. Try to search some diy sites to figure out how long you will need to expose the film with your particular light.
4. Wash out the screen. The parts that were under the black parts of your screen will wash away while the exposed parts will not. Hold the screen up to a light and check so there are no emolusion left in the design.
5. Let the screen dry. Speed up the drying with a hair dryer. Not to long in one spot though....
6. Print.
7. If you used plastisol inks you should bake the shirt in your oven for a little over one minute in 160 C. If you used some kind of water based ink some (all) will dry by itself. However you need to iron the backside of the print to fixate the ink.
8. Done.
Edited by Lars on Feb 6, 2006 at 05:09 PM
0 -
I don't know the weight of bape now, but back in the day they used oneita t´s.Quote:Hi,
Expecting to sell and market. Looking at $30 a tee and $79 for hoodies, what would be the best quality? like what quality does Bape use?
Thanks,
Steve
--- Original message by Nismofob on Jan 23, 2006 10:41 AM
0 -
Will the rigid premium jeans stretch with some wear?
0 -
Hello, I'm new.
http://www.bargainsavenue.com have 501 stf for 33.99 USD. International shipping isn`t expensive either.
0
NICE "BAPE" TEE................FROM FRESHJIVE
in supershopper
Posted
I fail to see the point of those tee's..
I'm very much looking forward to the Freshjive x Hot Tuna collab though. It's gonna be hot so don't sleep.