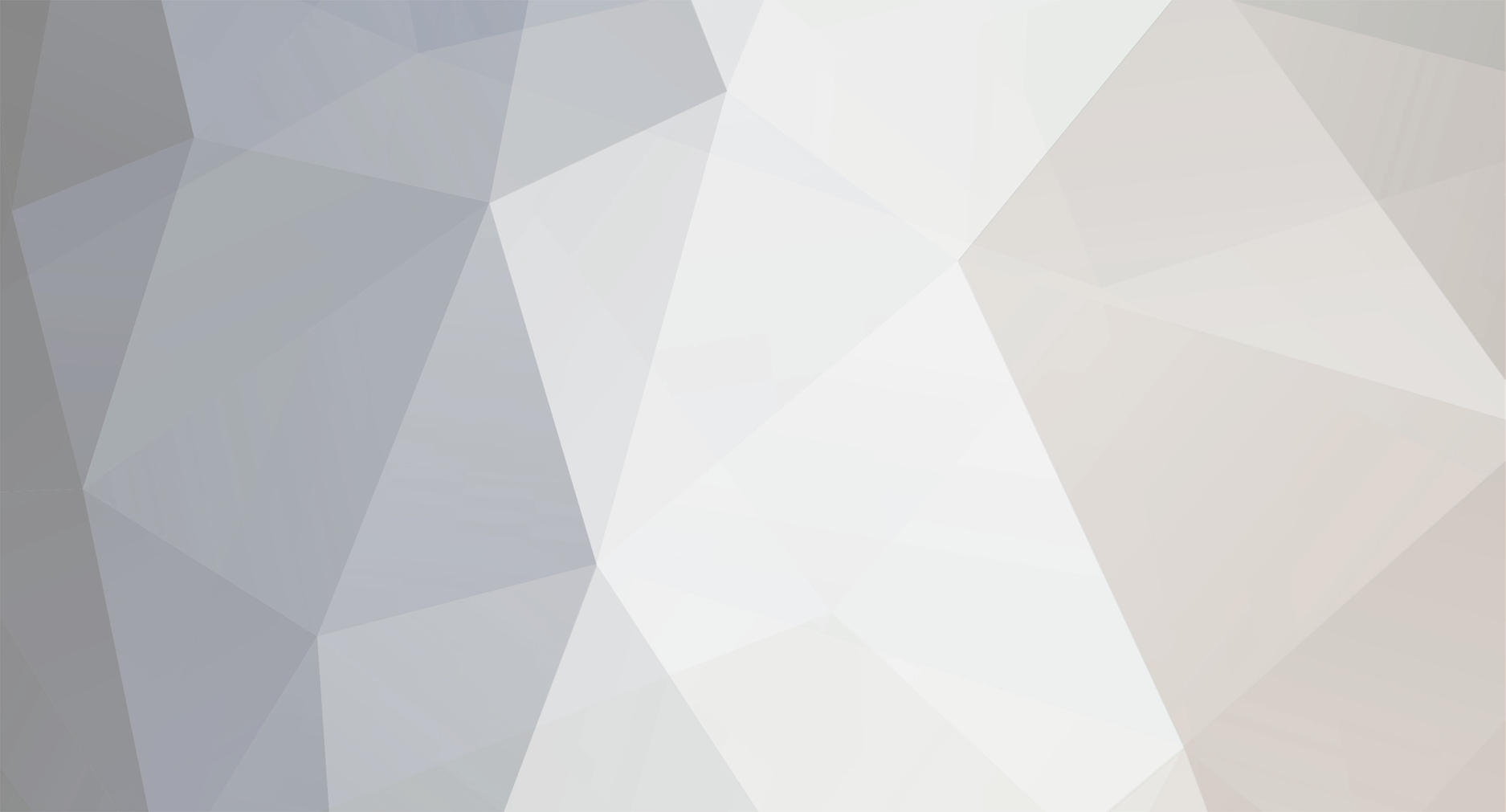
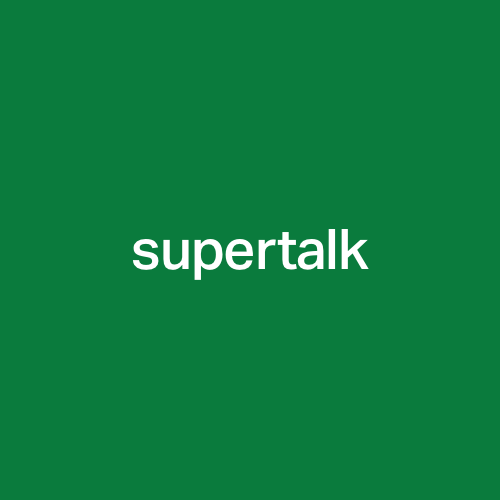
ringring
-
Posts
1135 -
Joined
-
Last visited
Content Type
Profiles
Forums
Events
Gallery
Store
supertorial
Classifieds
Posts posted by ringring
-
-
then i'll be raiding the log cupboard and getting the logwood prepard. I think i'll have enough.
If you have anymore suggestions / comments / hints / advice etc please let me know before it's too to change anything! I think this is a bit of a hit and miss experiment to be honest, i'm just going to jam it all together and see what happens.
.
Thanks for the photos! Is that Logwood? aka Campeche/Campeggio? Anyway, you may want to start processing the wood into chips/sawdust plus whatever else that you can find with tannin content (acorns, pomegranate peel, rosehips, chestnuts etc) and soak them or even boil them up to accelerate the process. Whilst chipping up your wood, you could see if the contact from the iron cutting tool will turn the wood black. It would probably work best on fresh wood.
And, as you have the iron & tannins, perhaps have a go at making ink?
http://www.knaw.nl/ecpa/ink/make_ink.html
You could test some bits of fabric by dunking them in the tannin liquid then into the ferrous water before making up your mud. You're doing a great experiment
.
ur amazing ringring :8) so the sunrise jeans would be a indigo/black/(temporary?) brown dyed jean? i wanna see how dralfs will fade.
From the photos at Blue in Green, the Sunrise jeans look to be blue, with a over dye in black done on the garment stage. The mud-dye will have taken especially well to the weft yarns, which I assume would have been ecru. I'm not sure how they'll fade - perhaps a little like the 45rpm Nandos which are indigo warp, sulphur black weft.
.
0 -
Ed has a pair of mud-dyed Yen Jeans.. Dying process
.
Thanks for that link. It's really interesting, seeing the garment dye process. Presumably the plum tree dip provides the tannins and the 'rice paddy' -like mud provides the iron.
I noticed that Gilded Age also produce jeans using various natural dyes. They have a nice account of their volcanic mud dye jeans here.
http://www.gildedage.net/volcanic_mud_dye.html
Again, the dyeing is about the reaction between iron & tannins. They also list other jeans dyed with Logwood (mentioned previously in this discussion) and Alder. Alder has a long tradition as a dyestuff used by Native Americans and may have some etymological relationship with the word 'black'. Alder bark was called blec by Flemish dyers of the Middle Ages and to dye using Alder was to 'blecken' - black being the colour that Alder bark imparted on wool.
This tree dyeing jeans is interesting
I know that sawdust from the Chestnut tree will make excellent dyestuff and was a substantial business in pre WW2 France and Italy. And I recall seeing beautiful blue-greys dyed with Sumac galls in Japan (Kyoto?), and wondering what kind of substance the galls were made of. Were they plant or animal? As it turns out, they are both!
You can see what I mean when you see them : http://feltcafe.blogspot.com/2007_10_01_archive.html
I think I may have seen them in traditional Chinese pharmacies too.
He can't have if he is doing it right. Read ringring's post: it will take at least a month to prepare the mud properly. I need more ringring in my life. Your posts are gold..
Thanks for the encouragement. Please note, it's purely an interest, and I'm just a dilettante, so please beware of any armchair punditry on my part. I'm not sure that the recipe for spiking the mud with iron from rusty nails is quite in keeping with the natural spirit of the mud dyeing - or if indeed it will work!
I'm delighted that dralfonzo is giving it try though.
.
0 -
is there anyway to get dr. bronners in europe?
There's quite a few places on the internet for Bronner's in Europe eg. http://www.dreadworx.co.uk
But there's no need to be so brand specific. Any pure soap will do. Look for Castille soap or Savon de Marseille. Many health food shops sell them. If you buy them in bars, then just use a cheese grater to break the soap down and just use as you would a regular washing powder.
0 -
The jeans would need to be rinsed clean afterwards.
0 -
I might give it a try tonight. How long underground do you think they would need to show some nice dying?
Excellent. A taker. I'm impressed by your enthusiasm.
I *think* a week under the mud would do it. I have no expertise in this, so I would be fascinated by your experiment.
You'd need your mud to be right though. So you may want to prepare it by soaking your rusty nails in vinegar (classically, 12 pints of vinegar to each pound of iron). Leave for a month. Then throw in your tannin plants. Oak bark, acorns, connifer bark (Navajo style), mascerated and left for a week.
Then make your mud and bury.
0 -
^ yeah thats nuts LOL. thanks for the insight
, +!!
You're welcome. Would anyone be up for some DIY mud dyeing?
The ferrous content could be met by soaking some iron filings or iron nails in vinegar. And the tannins could be introduced by using oak bark, acorns and/or oak gallnuts. Very traditional
Mix with earth and water and bury your jeans.
Could be an interesting experiment.
0 -
http://blueingreensoho.com/site/index.php?page=shop.product_details&flypage=shop.flypage&product_id=4319&category_id=&manufacturer_id=47&option=com_virtuemart&Itemid=28
SunRise Japan Jeans
does anyone have any info on them? what is "mud dye"?
I have not yet seen the jeans in question. Presumably the indigo is yarn dyed as is the normal practice for denim, and the the mud provides a lo-fi black 'topping'? I'd be curious to see if they were skein, piece or garment dyed in the mud. Blue in Green consistently find interesting stuff.
Despite my ignorance regarding your first question, I can chip in with a small contribution to the second part of your query.
Mud dyeing is an ancient method to achieve black before the global trade in Logwood* in the 1600s and the use of sulphur dyes a couple of hundred years later. It's a way of dyeing found in all over the world. Perhaps these jeans are mud-dyed in the Ryukyu areas of the south of Japan where the tradition is preserved.
It all depends on the right type of mud. Burying your jeans in any old muddy ditch will probably just get them dirty rather than imparting any colourfast tonal changes.
Two conditions are required in order to get a mud that dyes: A high ferrous content, from water passing over iron-rich rocks and a high tannin** content from rotten vegetation. Boggy mangrove swamp mud, paddy field mud where the water gathers in rust tinged pools. The iron and the tannin react to form a black dye.
Perhaps any Kiwis reading this can confirm that the the black flax used by Maori's for their traditional costume was achieved by mud dyeing. I can't help but wonder if there's some cultural connective tissue that binds Maori mud 'paru' dyeing to the New Zealand All-Black rugby kit.
*As a footnote, the story of logwood dyeing is an epic story, that warrants a deeper discussion, encompassing the Spanish discovery of the New World and the Mayan people put to the sword and yoke to process this precious black. Of English pirates and privateers. And the spread of Puritan religious values which favoured sober, black coloured clothing over the perceived rich indulgence of a more colourful palette.
** Tann come from Celtic word for oak. Oak is traditionally used to tan leather and in conjunction with iron mordants, to dye yarn/fabric.
0 -
Sanforized jeans oten, I believe, have more starch applied. But most people wouldn't bother soaking them. I seem to get more thread breaks with LVC 47, even after waoking, than I do with my Sanforized Lees.
INdigo by the way is not water soluble. It's mainly abrading that removes it. But - and we need ringring here - by belief is that some indigo doesn't dye the cotton properly and just sits on the surface, that's what you will lose on your first soak.
I don't think a hot soak will partiuclarly lose more indigo, it will merely give more shrinking in unsanforized fabric.
I don't think sanforized jeans will be starched any more or less than shrink-to-fit jeans. The starch is just used to strengthen the threads for the weaving process. Sanforizing is a separate process that occurs after the fabric has been woven.
Indigo dyeing is a little like dipping a doughnut in sugar. Some of it sticks and some of it doesn't. So yes, that's the stuff that comes away in the first soak.
0 -
Yes, those were the jeans I referred to.
You may want to look at Samurai's S5000VX 21oz jeans then. Closer to the SD103 cut.
0 -
I don't know what BIG has, but I remember that the gentleman in the Osaka SDA store describing the 21oz jeans as '101 cut' and seeing them worn confirmed that.
Unfortunately, I don't recall the model number, so am unable to verify if the ones I saw were SD1405.
0 -
Anyone knows more about this?
http://item.rakuten.co.jp/bluemarble/dartisansd1413/
Very interesting indigo color but I can't find info elsewhere about this...
I've seen them. Vivid blue indigo, (if you'll excuse the pleonasm), which from the pink flowered plant photo in the link, appears to be from Dyer's Knotweed, Polygonum Tinctorium. The indigo plant from South China/Vietnam, that's cultivated in the Tokushima district.
Unlike some of the top end natural indigo offers from other Japanese 'repro' brands (eg Pure Blue, Samurai) , the denim is relatively flat in texture. Very different from their SD101/103XX natural indigo jeans, which are far more understated.
0 -
Anybody has experience with the new d'artisan 21oz denim ?
I read somewhere the cut was the SD103 one, which I own and find great, but according to BiG size table the rise and upper thigh are bigger, for a 32 :
SD 103 rise : 10.75
thigh : 12.5
For the 21 oz :
rise : 11.5
thigh : 13.25
Is it due to the 21 shrinking more or really different cut ?
The latest 21oz version that I've seen was based on the 101 cut. Longer rise, 'hips' and carrot leg. Really nice, dark denim, with a slight purple tinge, much nicer fabric than their original 21oz. Great, thick leather patch.
0 -
You're both correct, the Euro version uses fully-felled seams while the Jap version is selvedged. Mine is the Euro with fully-felled seams. I'll snap a pic of that as well when I get home tonight.
I was referring to actual 1940s vintage Wranglers, not reproductions.
Although, whilst on the subject, I'm sure that Warehouse do one of their Diggers with a 'felled selvedge' outseam. It's not a true fell seam, but rather a selvedge outseam where the edges have been folded over in one direction only (as opposed to being ironed open) and then double stitched like a fell.
I've always been interested in Wrangler's reputation amongst cowboys as being tougher than Levi's, and more of a working jean rather than a fashion item.
0 -
I doubt they'll shrink at all. I wouldn't bother. The starch that's in them will help you get a good fade, too. Hot water won't damage Sanforized jeans - it's just that there's no real point in using it, given the fact they're preshrunk.
The fact they're non-selvage is irrelevant, these jeans were never selvage, but it's still good quality denim.
I'm fairly certain to have seen geniune 1940's Wrangler's with lefty selvedge denim, replete with 'Levi's' style arcuates.
These repro's look lovely. Look forward to more photos.
0 -
They are very nice jeans. Beautifully made, lovely denim and very nice details. Better if anything, this time 'round than when I saw them a couple of years ago in Los Angeles.
They are Duckdigger-ish and are represented in were in quite a few places in Tokyo, including Warehouse, although they were strangely absent in Warehouse's hometown stores.
The last time I saw them, was in the wonderful Restore Nomori shop-cafe-bike emporium in Kyoto.
Diggers with a modern fit.
0 -
PS - I think there are plenty of books on Lowell - I read!
0 -
I remember thinking that your english denim statement was quite a bombshell - very subtly dropped, like a velvet cosh.
Then you starting this thread about mills led to pieces being put together....
I'd also love to see a period piece of english denim. Perhaps an enquiry to the V&A is in order....
I'd be interested to see that French catalogue too.
Nice mention of 'nim'. Great work Paul.
0 -
Talking of Lowell, there's an interesting tale about how rubber soled shoes were invented.
It comes from an Irish immigrant calico printer working at Lowell. Apparently the looms vibrated the floor on which he worked and he had taken to standing on a rubber mat in order to dampen the vibrations.
The problem was that his idea was so good that his rubber mat kept getting stolen. So in order to foil the thieves, he cut up the mat and nailed the rubber to his shoe.
For this little flash of genius, 3 years later, in 1899, Humprey O'Sullivan was granted a US patent for rubber heels and started the O'Sullivan Rubber Company - which should be still active today.
Another little Lowell story, which you could perhaps verify with your parents, is that the mill was a product of industrial espionage. Francis Cabot Lowell had visited mills in Lancashire, England and tried to license their technology. He was refused. But Lowell had a photographic memory and managed to reproduce the water mills and all their machine on his return! - he also sneaked out some sketches of the machinery.
Paul - thanks for the Cone write up. Fascinating, all of it, particularly the period of modernisation, with the introduction of sulphur dyes and open end. The open end wash look is also known as 'salt & pepper' in addition to 'marbled' & 'orange peel'.
This thread prompted me to think back to your book. The passage where you described the origins of denim..
"Quite possibly the missing link came from the textile mills in Lancashire, England, which by 1800 were producing a fabric named denim, made out of cotton and probably designed to echo the look of French wool/silk twills."
I remember thinking at the time that this was a very important fact you were tantalising us with - that denim is english!
I know that the English had been selling cotton twills named as 'De Nime" to give their product a fancier sounding name, like calling a custard pudding 'Creme Caramel'. The breakthrough that transformed the original wool mix Serge De Nime and Fustian (Fustagno) fabrics into denim, was English.
These fabrics had been mixed with cotton - Fustian was wool warp and cotton weft, because up until Arkwright's invention of the Water Frame, no one in Europe had been able to figure out a way of mass producing a cotton thread strong enough to be the warp.
So, with Richard Arkwright's invention, English mills were finally able to produce all cotton twills - and with their access of indigo from US and Indian plantations, denim weaving was made possible.
I wonder if it was Arkwright's hairdressing background that led him to the eureka moment of first stretching the cotton before twisting it, in order to produce a warp strength yarn.
.
0 -
Talking of carding and Scotland, I'm sure I've seen carding machines composed of racks of Scotch Thistles heads (which explains their genus - Cardus)....
0 -
Thanks for the recipe and the proverb ringring, I can't wait to try some crottle-dyeing. So the wool is dyed before it's carded?
Traditionally, yes. Dyed and then carded. The recipe I listed is very much a home-brew, lo-fi version, but nevertheless a traditional method used for lichen dyes. You can also do it by boiling up the crottles separately for a few hours and then dyeing the wool in the strained liquid.
Across the pond, the Navajo were using lichens to dye wools for rug making. A kind of Native American Tweed
You're right about the home-weaving. I always associate the word 'mills' with weaving.
I agree about Skye - a haunting place, whose colours (and smell - if you do the crottle dyeing you'll see), are reproduced uncannily in the fabric.
0 -
I'm interested in what the mills actually do - presumably just wash and finish the fabric. Does anyone know?
Presumably, they just weave and finish the fabric. The spinning and dyeing would be done elsewhere, locally.
I wonder if they are still Crottle dyeing any Tweed yarns?
As a bit of fun for anyone going up to Skye or the surrounding areas, you could try your hand a dyeing with Crottles (what a delicious mouthful of a word), the leafy, seaweedy, lichens that grow on coastal rocks.
There's a gaelic proverb from Skye that goes something like "better a rough stone produces something, than a smooth stone that produces nothing"
Contact dyeing is one of the easiest ways to colour wool using a vegetable dye. You just need a pot, wool (pick clumps off barbed wire fences), some soft water (rain water or even day old urine) and your crottles.
Layer the crottles and and wool in the pot like a Lancashire Hot Pot or Lasagne if you like
Bring to boil and simmer for an hour or a few hours, depending on the shade desired. If you leave the wool in the pot until cool, then the colours will be even darker.
Nice find with that Amoskeag factory song. Music & mills
0 -
There's an intriguing radio program with lost of relevance to the denim industry broadcast today, and available on the BBC website, about Harris Tweed.
An interesting link between Tweed and denim is of course in the name. The name Tweed is widely believed to have come from the misreading of a fabric invoice around 1840 on which was written the word Tweel (twill).
Twill is said to have come from the french word Touaille, although I do wonder if Toile would be more appropriate. Denim is a twill weave, and also a derivative from french - Serge De Nimes.
Gene/Jean Fustian was the hard wearing, indigo dyed, twill cloth woven in Genoa, which was imported to England as early as 16th century giving rise to the name, blue jeans.
More wittering about that here : http://www.superfuture.com/supertalk/showthread.php?p=264210#post264210
It's years since I've been to Skye, but I'd thoroughly recommend a road trip by car, and to catch as much of West Scotland as possible.
0 -
You're the teacher sir
I am interested in the historical threads that draw many events together that have shaped the way we view our world today.
From the cradle of capitalism (the industrial revolution, new industrial towns, global trade) blossomed a few seeds of socialism.
You have the French Revolution in 1789, and just a couple of decades after, Robert Owens fathered the Co-Operative model in the Lanark Mill.
A couple of decades after that, Marx & Engels publish their Communist Manifesto on the eve of revolution.
These are events, hundreds of years old, that still reverberate today.
0 -
Partytaco - great link to another great story.
Paul - You're Superfuture's first Loomnerd
I don't have a copy of the 1904 Draper catalogue LOL.
You are tickling the lovehandles of another fascinating subject, the late-Georgian/Victorian utopian mill towns.
Hopedale followed Lowell - whose 'utopian' mill town had the pragmatic result in attracting young women workers from the surrounding area.
Which was preceeded by Robert Owen's New Lanark Mill - which introduced labour laws that we would recognise as modern today.
Then there's Titus Salt's (best name ever?) Saltaire, which is now a lovely place to get a cup of tea (and a dose of Hockney), in God's Own Country. Amazing place.
0
Sunrise muddyed jeans/On mud dying in general
in superdenim
Posted
Excellent. I hope you keep us posted with your results.
I couldn't help noticing that you're from "the cancer-causing-capital of the confederacy" and thought you might like to try a home brew version of dyeing using walnuts. Why walnuts? It's the dye used for the uniform jackets of the Confederate soldiers in the American Civil War.
You'd need the husks of the fresh nuts and steep them in water to ferment them for a week or two. Throw in some walnut bark if you like. Then chuck in your Tshirts or Jeans. Cold dye or warm dye should both work.
And if you have a passing interest in military uniform, apparently the US Army used Osage Orange to obtain khaki colours prior to switching to synthetic dyes. I've seen this wood used in bows, knife handles and skateboards