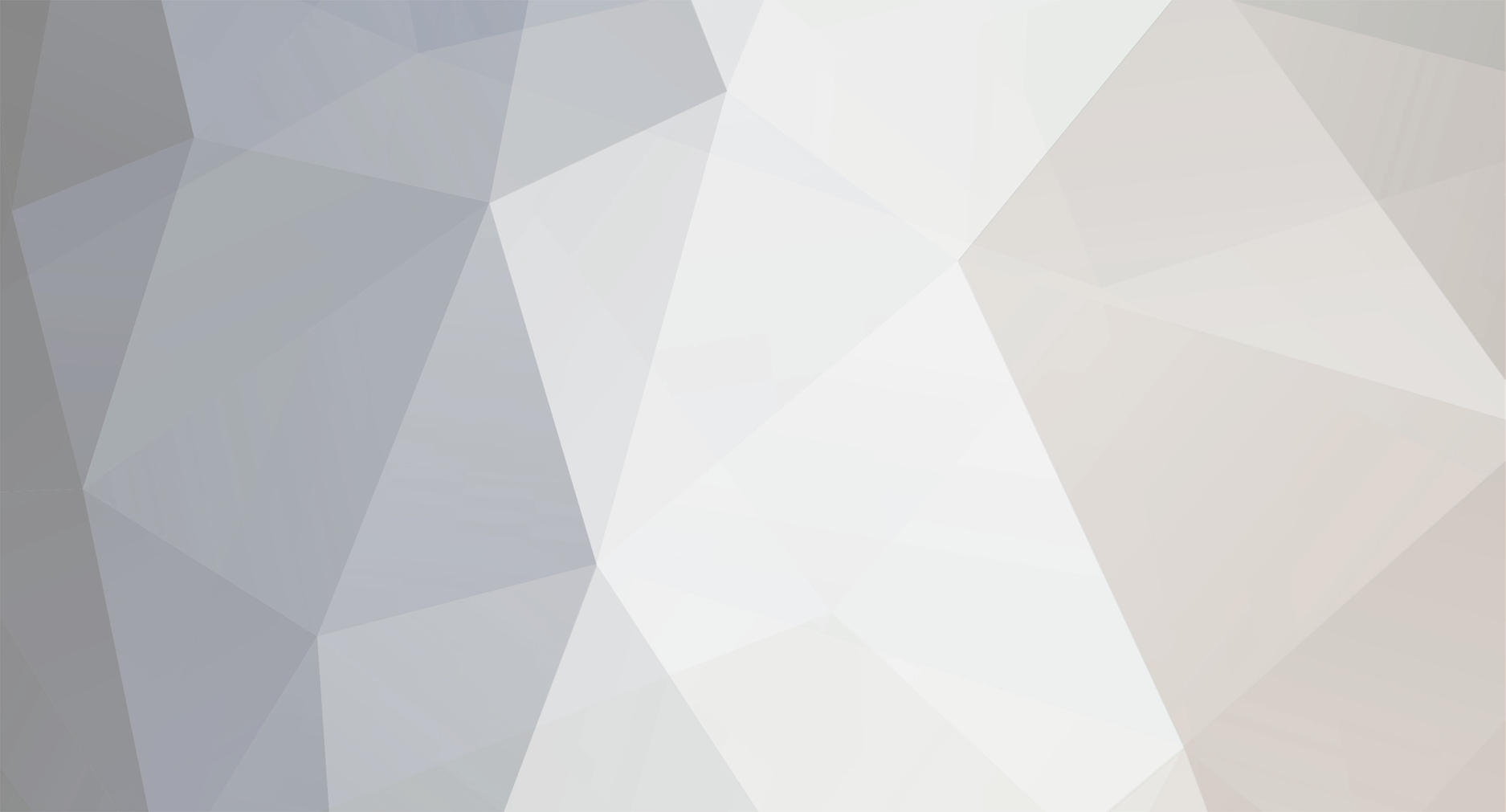
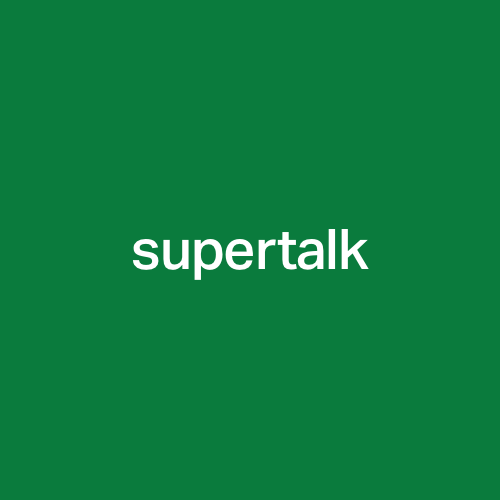
ringring
-
Posts
1135 -
Joined
-
Last visited
Content Type
Profiles
Forums
Events
Gallery
Store
supertorial
Classifieds
Posts posted by ringring
-
-
Sad to hear about Interstate.
Regarding, Son of Stag, Rudy has always been very pleasant and generous with his time & advice.
0 -
epic.
2 -
It seems to me that this contest was about three things:
1. The journey.
2. Sharing an experience.
3. A beautiful pair of jeans.
Congratulations Daniel. You nailed all three.
11 -
thanks for the interest in this conversation. snide remarks aside, I'll be happy to do the legwork on this and I'll make it transparent - you'll all be able to see that I assigned your votes the way you wanted them. Okay so:
1. we are going to have a popular vote pick the top five and then have carl chiara, ralph tharpe/roy slaper and ringring choose the winner from that selection. [a query: why sideline roy? i figure he and ralph are really the "creators" of this contest so they both deserve a nod. i am, however, fully willing to be overruled on this.] The three judges will then communicate amongst themselves to pick the final winner. Another thought: there seems to be a lot of interest in having factors outside of the final appearance of the jeans (e.g., thread contribution, photos, adventures, etc) be a factor in determining the winner of this contest. However, none of the judges are likely to have this perspective since they haven't been part of the thread - I assume they'll be much more inclined to make the decision purely on appearance.
It's the journey that makes these jeans interesting. So best stories + best looking pair = win. At least in my book.
2 -
Good to see you back in business Ande Whall.
1 -
Welcome back Paul & a happy Thanksgiving to all of you.
Loomstate & marketpeople.org look great
0 -
ringring himself!
Those SExRRxFH are beautiful.
Your FH's aren't too shabby either. Pink T & Palladiums. Nice.
Look forward to new pics.
0 -
SExRRxFH
They are looking beautiful. Thanks for the updates. Very happy.
0 -
We are pleased to announce that the elusive RingRing will be interviewed for the film. This is the most recent in a series of big "wins" for us. Thanks tho the person involved for making this happen (sorry, I wasn't sure how much I was allowed to say).
??...............
Good luck with the film.
0 -
Ringring post from 6 years ago re: Ironhearts.(On page 5 of this thread.)
It came true! (Wearing a pair as I type...)
6 years. That flew by.
0 -
jeans are washed and dried, shrank to fit good, bath looked like i had boiled smurfs in it, but surprisingly little movement on the jeans, will take pics of them when the sun is out tomorrow, today me and my ROY boxers got crafty
testing glues on neoprene
then, what to do with stacks of old tees i cant be bothered selling
baby goth
This + kayak = exceptionally cool. 'The creative mind plays with the object it loves'.
.
0 -
Hem-stitching. It's done with a special machine that I don't believe has been manufactured for non-commercial use for a long time. It punches a hole in the fabric, then stitches the edges closed. Put a bunch in a row and you have a stitch. I think it mostly used to be used for linens and curtains.
Roy got this machine a while back, and was really excited about it. This is the first thing I've seen him make using it.
Was going to say, Roy6, that I swear I had seen something like that on curtains or old hand towels...Yes, it's called fagotting, and as you both have noted, sometimes featured on curtains, table linen, pillow cases etc as well as apparel.
Machines are still manufactured for this process.
0 -
Welcome killer b - and great first post.
Sansome - Here's a link to the British Library's collection of newspapers.
0 -
ringring.. maynard..bluegold..and entertainment- thanks for the leeds and the kind words! I would like to know where the tin mines were in the U.K? It's my guess right now, that the Neustadter Brothers would have marketed clothing to the miners? I would like to look in a small newspaper that was around the tin mines (if one existed?) I photographed one of Brit Eaton's, turn of the century, Neustadter Brother's shirts with a made in England label. BTW Neustadter Brothers had an office in New Zealand and Yokohama Japan in the 1890's. Guys thanks again for all of your help:)
Eltopo, your pants are looking good.
Tin mines were dotted around Devon and Cornwall in England. There are plans to re-open the South Crofty mine in Cornwall.
For sure there would have been Devon and Cornish newspapers in the 1800's.
The Exeter Flying Post and Cornish Advertiser are listed here:
http://www.jisc.ac.uk/media/documents/programmes/digitisation/jisc_19cnewspaper_map_04.pdf
.
0 -
Thanks ringring, lots of research to do. Do you have any idea about 1800's English newspapers online? I was wondering If I will have to go the Libraries in England, to do my research? Thanks bluegold.
I'm sorry I don't have any links to online English newspapers from the 1800's.
I think you're doing groundbreaking work, which will influence denim fans for generations.
I'll repeat the quote from the wonderful Paul Trynka's book,
"Quite possibly the missing link came from the textile mills in Lancashire, England, which by 1800 were producing a fabric named denim, made out of cotton and probably designed to echo the look of French wool/silk twills."
Paul was onto something.
Please follow your instinct across the pond to England. You could start at the British Library, then the British Museum and the Victoria & Albert Museum before heading north to mill country.
Before you go, it may be worth looking in the National Museum of American History in Washington, for the 1810 18th edition of the The Repository of Arts, Literature, Commerce, Manufactures, Fashions & Politics magazine.
And John Harper's The Weavers Draft Book of 1792, from the American Textile History Museum in Lowell (?)
Good luck!
0 -
I agree. Awesome!
Love the chinos (lovely khaki with the alum - I guess you'd get greys & blacks using iron) and the Catappa & Mangosteen tees.
0 -
The book is going to cover many clothing manufacturers from the 1850's to the 1930's, East and West coast. A very large Levi chapter filled with all sorts of new information, all of the research so far points to XX starting in 1876, just like the 1901 catalog says ( XX 25 years the standard) I am interested in European denim, I know Neustadter brothers and Heynemann had offices in England... Do you know about 1800's denim in Europe?
Really looking forward to the new book sir.
There's been some speculation about English denim on here..
http://www.superfuture.com/supertalk/showthread.php?t=143701&page=5
.
0 -
Since we are on the topic of Asam, i have another suggestion for you..! I'm familiar with the use of Asam as it is frequently used in my household(I am half Peranakan.) , and another ingredient comes to mind.
Bunga telang or the Clitoria ternatea. Peranakans frequently uses this flower as a form of food colouring for our desserts. It creates a nice indigo-ish shade of blue too..! just thought you might find it interesting.
Nice to see the 'pussy pea' making an appearance
.
0 -
That's correct, but tanin concentration in Mangosteen is rather low, I found much greater tanin content in Terminalia catappa. It produces similar shade to South American Logwood. I used iron mordant before mangosteen bath to darken the color.
Very interesting ringring. Yes, Asam Gelugur is also known as Asam Jawa, and it is not very popular as dye because its main use is for spice and food coloring here. Definitely will try it someday.
I have some silk fabrics and wool yarn to dye out of curiosity, but my main focus is in linen and cotton.
If it's any help, unripe Mangosteens may have a higher tannin content.
What part of Terminalia Catappa are you using? The fruit or also the bark? Always with an iron mordant?
Have you tried Terminalia Chebula as a dye? It's supposed to be particularly tannin rich.
I like the comparison with Logwood - I guess various members of the Terminalia family were the Logwood of Iran-Africa and right across India-China-Malaysia-Vietnam.
PS. I thought Asam Gelugur was different to Asam Jawa (Tamarind)?
.
0 -
Other than indigo we also do other color, we just achieved a beautiful shades of grey from a mangosteen this evening and hoping to apply it to a shirt. I'll post the pics later.
you can see more detailed pics at our flickr http://www.flickr.com/photos/bluesville
I'm greatly enjoying your posts and looking forward to seeing the results of the mangosteen dyeing.
I'm guessing the the tannins from the mangosteen skins are the active dyeing agent. Are you using anything else with them? eg. something with iron content to provide the black tones.
Will you also experiment on dyeing animal fibres, like silk?
Mangosteen's (Garcinia Mangostana) cousin, Asam Gelugur (Garcina Atroviridis) is used with turmeric, tamarind and a bit of alum for silk dyeing. All boiled up.
0 -
Good to hear you're safe Ande. I've been quietly admiring your work for years.
It's uplifting to see fellow Superfutarians gathering round to look after their own. Altruism is possibly the most noble of human qualities. You have fans and friends here.
So a bump up, and another donation inbound.
Keep your chin up, get back on your feet again and keep doing the great work.
Dear Sufer's,How are you all, hope everyone is good out there in denim land.
Unfortunately the worst news regarding the condition of the workshop came in yesterday. The building has been very badly damaged in the Earthquake that struck on Tuesday the 22nd of February and is set to be demolished in the next week. Earthquakes are a hell of a thing, it's taken over 200 lives, my home, workshop and I still can't find me little cat.
I have to thank my good fortune that all friends and family are safe, and that I wasn't walking to, or in the workshop during the Quake. The workshop is in a cordoned red zone, as well as a super cordoned "No Access Zone' in the worst hit area in the central city, shadowed by a large hotel that is on a lean and will have to bought down in the near future. Some business owners will be allowed access to their buildings to salvage gear, but not in this very dangerous no access zone where the workshop is situated. For myself and others in this terrible situation, the Urban Search and Rescue squads are coordinating with bussiness owners to salvage what they can from the premises before the building is demolished. The 'smash and grab' allowed lot for each business is approx 5-10 minutes and a 44 gallon drum to fill with the most important items, which has been relayed to the Urban Search and Rescue guys by the business owners. But there are still no promises that they will be able to salvage anything. They will try their best, but if there is any danger what so ever they won't take the risk, which is a fair call. I have given some good instructions about trying to grab pattern drafts, labels, hardware (there may be thousands of buttons and rivets scattered across the floor however) and the denim, which may not be able to saved as it's quite heavy and won't fit in the 44 gallon drum. Everything else, machines, patterns, tools, computer and stock will be crushed with a wrecking ball and digger. It's a hell of shame indeed.
So much time building this small denim business will be lost for forever. Money just can't replace some things that have taken years of work and collecting. All the old sewing machines scrounged and bought back to life. Sewing machines like the Durkopp keyhole buttonholer are as rare as hen's teeth here in New Zealand, affordable old ones that is, brand new ones are 8-12K. Another most unfortunate situation is my insurance had lapsed and I was going through the process of finding a new company, stupid, stupid bugger I am...took to long, pissed around and procrastinated about getting it done.
After having said all that....I will be back fellas! I just have to start again, having done it once, I'm sure it won't take to long before I will be back in action getting the hand made jeans to the people. I will need some time to organise things, get a new home, most probably with a workshop attached, in a garage or a big house. There are limited good spaces left in the city, and homes are in short supply now too. I don't really wish to live/work in the city anymore anyhow, to freaky and it will be a long time until it is back up and running. It may be cordoned off for months while they demolish nearly 150 buildings.
There are some immediate problems to overcome to get back in action. Finding a good place to get set up again will be the first step, I am staying at my brothers house at the moment, which lucky escaped any Quake damage. The next step will be gathering suitable sewing machines and trying to pay existing bills to avoid losing essential suppliers. If the patterns, labels and hardware can't be recovered, there is a ton of man hours to re-cut patterns and money to replace hardware and labels. I really don't think the USAR guys will be able to rescue the denim, such a shame as the two 50m rolls for the contest had just come in and also the 50m of the Special Roll denim, four days before the Quake hit. My supplier in Japan sends me the denim when I order it and I make payment on the 20th of the month, or later, he is a super mellow guy and we have an unwritten contract based on trust. So basically I need to pay for the 100m of contest denim to keep me in good stead with these great denim makers. I have always been rubbish at asking for help, I find it quite embarassing and don't like to put people out. I am going to put up a $20 'save my bacon Earthquake messed up the AW jeans production and needs to pay denim bills' rescue fund on the website. So if you have a spare 20 bucks lying around it will definitely be going to a good denim cause. I run the business on next to nothing and put all earnings back into it. Not really the best way to work, always fighting off the ropes, but was the only way to make progress with new garments and branding etc. I had patterns and labels ready to go for new models of jackets and shirts that were in the final design phases. Heartbreaking really, they never got into reality.
Thanks very much to all of you who have supported me over the years, getting a bit choked up now about years of awesome Sufu guys, extremely funny, interesting and bouncing around all kinds of ideas. And the Superfuture creators themselves, great guys that have made a special place for all of this to happen. The best part of my job is hearing your feedback about the jeans, your stories and just having great chats. By no means will I ever give up on the label, this denim thing gets in your blood as you know, haha.
The Workshop is in the red 'no access area. Whole blocks around this area are going to be demolished.
0 -
This is from our earlier experiments. It's pretty difficult to dye a wide fabric, say 2 meters wide. In order to make the the dye spread evenly across the fabric, it's important to make sure the fabric doesn't fold.
as you can see in the pic above, there is some area with different shades and the indigo isn't spreading evenly. It's mainly due to the fabric being folded when they're dipped into the medium (we use a 1,5 half meter tall plastic barrel with approx half meter diameter). The barrel isn't big enough for the fabric, so they're forced to fold inside. Usually the folded area in a fabric won't absorb the dye nicely, thus the color isn't distributed nicely. So if you guys want to dip some wide fabric, it's better to search for a wide medium, or better, use your pool/jacuzzi for it
(some batik dyers in Java are actually using a small pond for fabric dyeing)
ringring
thanks for the explanation. I'm also planning to dye from the yarn state and right now I'm still searching for a master weaver to weave my dyed yarn in the future
I also luckliy got my hands on the beautiful indigo from Seiwa (i think it's a subsidiary from Japan Blue). Its pretty expensive ($20 something for 10g indigo - compare to my source, $5 for 1 kilo), but it seems of a very high quality. Maybe i'll try to incorporate them in my next dyeing session.
If it's any consolation, piece dyeing industrially is also fraught with un-eveness
0 -
fixed 4 u...
Thank you!
0 -
Congratulations on your book Paul.
Loved Iggy. Loving Bowie.
True, not entirely sure why. But on the plus side, the US version has more lewd stories, the UK legal read was insane (apparently, the longest in the history of Little, Brown).oops, sorry, what was Q?
These Roys are looking fantastic.
0
home-made jeans
in superdenim
Posted
Start by deconstructing an old pair. It's a good learning.