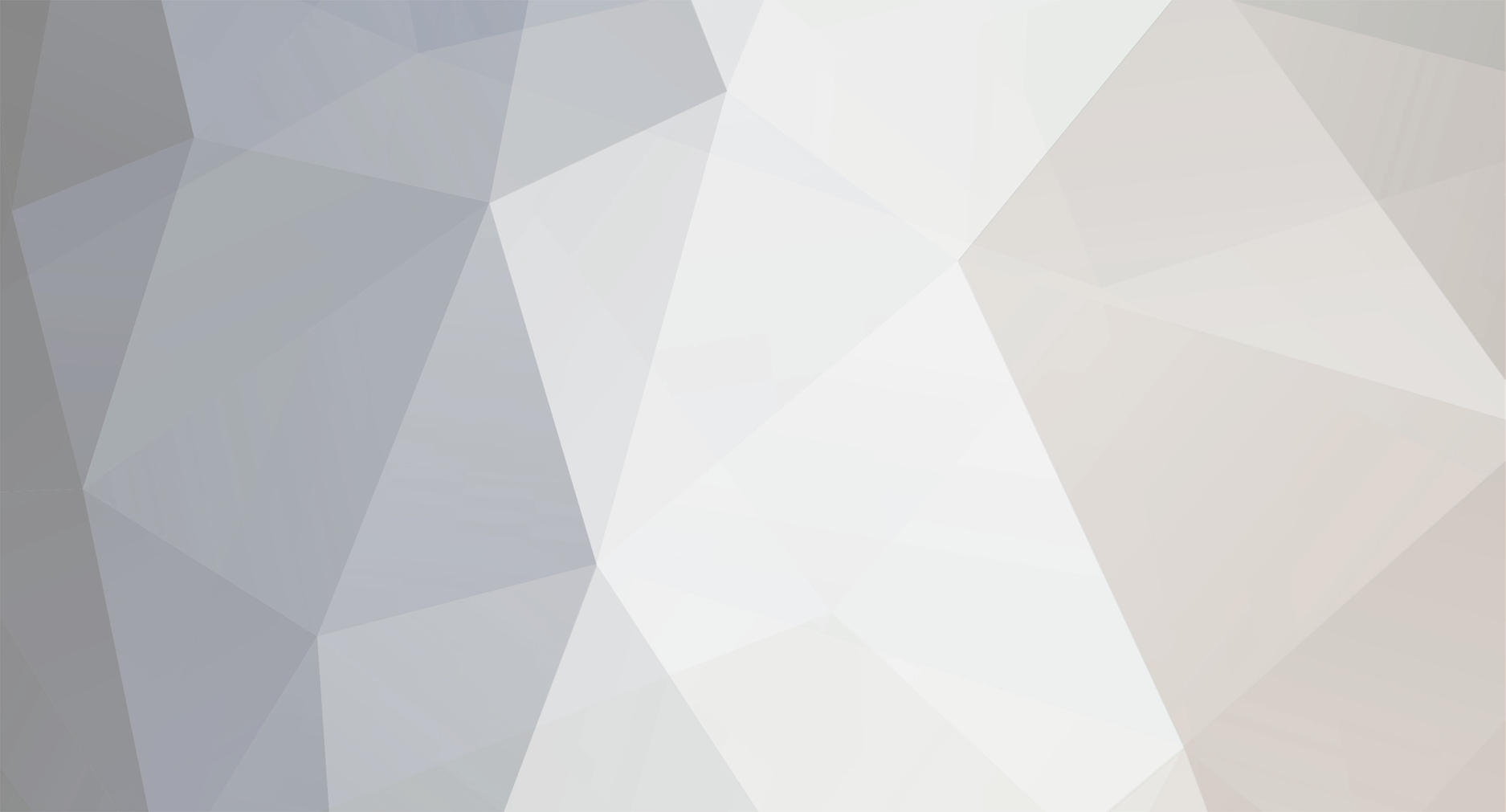
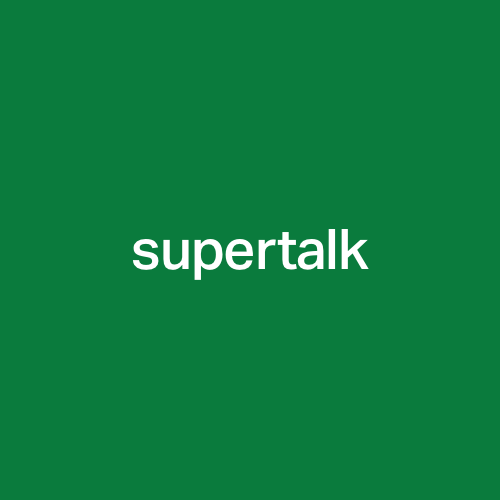
pacioli
-
Posts
322 -
Joined
-
Last visited
Content Type
Profiles
Forums
Events
Gallery
Store
supertorial
Classifieds
Posts posted by pacioli
-
-
Mike, is there any marketing on the garment to link it to Wo? I wonder if this fall under Wo's patent as I understand it. His description calls for the reinforcement to be a part of the pattern piece but that old-timey technical writing is always hard to understand so I can be wrong.
Also I have a couple of outlandish theories about Wo that I cannot fully substantiate. Let me list out some findings and musings related to Wo:
1. He did make a relatively good amount of money, if not a small fortune, as a result of the patent. From the Switchmen Journal (vol 7, issue 1, 1893) article "Fortunes in Patents": "An ingenious Chinaman, of San Francisco, named Cheang Quan Wo, made quite a pile of money out of a gusset for reinforcing the pockets of overalls." Whether it is by making overalls, selling the rights, or working out a similar deal like Jacob Davis and Levi Strauss....that is not clear.
2. The above article was repeated in Sept 1893 issue of Current Literature: A Magazine of Record and Review and Wo's name was butchered into "Cheang-Wang-Wo"
3. It is possible his name was spelled in English in various ways as he was obviously not born with an English name. But for the patent we know "Cheang Quan Wo" is used.
4. Is he Mr. Cheang or Mr. Wo? Either one could be Chinese last names, although variants of Cheang is more popular as Chung or Chang or Cheng, with and without the "g."
5. Is he of the leather shoe maker known as Quan Wo & Co. on 315 and/or 317 Clay Street? Don't think this was a popular name (?).
6. Is he of the Quan Wo Chong Company that was involved in 2 or more lawsuits in the 1890's (defendant against Lee Chuck; and Plaintiff against Laumeister related to bales of cotton)? If so getting those cases would shed much light.
You could mistake this for the Greenebaum brothers, but if the leather reinforcement pieces come from the seam, it's the Wo patent. I've seen both Greenebaum and Wo use leather, denim and I would assume duck reinforcement pieces ( i've never seen them in duck) I think both Greenebaum and Wo had a advantage over most companies, Levi had the rivet and Greenbaum had the pantent for any kind of material that over lapped the pocket seem. This meant that Greenebaum brothers could make a regular pair of pants and slap leather triangles over the pocket corners ( not much harder than just adding a rivet) Wo, was a little more difficult to make, next to Greenebaum. Levi, Green and Wo enjoyed this advantage for only a few years. Some time in 1877 or 78 the Arrow head stitch came into play and I believe leveled the playing field. We have found this Arrow head stitch on 5 companies so far( arrow head stitch is on page 71) I think this is one of the reasons for the Greenebaum brothers teaming up with Sachs and Freeman in 1878. Well the research continues.
0 -
Any mill willing can run 2x1. But since you mentioned currently, and I assume you mean selvage, the answer is the Japanese mills are doing it consistently. I don't shop Japanese lines so I am not sure exactly which one. Should not be hard to find out if you are in the market for some.
Pacioli,Any places you know of that are currently making 2x1 denim?
0 -
2x1 righty.
Is much else known about Wo?
I think this is the piece that you were talking about. It is light weight, some one should be able to tell if it's two by one denim?
0 -
Those Cheang Quan Wo...
beautiful indigo...interesting, left hand twill. Is it really that bright of a blue? Does the leather have a little blue on it or is it the picture? Love the uneven stitching. A fine specimen.
Are all your CQ Wo pieces left hand twills?
0 -
This was on craigslist NY and I've kept it all this time, for today I guess.
free surf boards (Financial District)
Date: 2010-04-13, 12:25PM EDT
Reply to: [email protected] [Errors when replying to ads?]
Anyone looking to hang ten this summer. I have been a professional surfer for more than 20 years and have ammased a huge collection of boards. I am moving to australia and have no place to keep them. Most are brand new. I am in lower manhattan pls call me to arrange a pick up JAMES xxx 598 xxxx
0 -
Just want to add to the praise here. One of the most refreshing things about Michael is his openness. He hides nothing and is not afraid to share details, pictures, speculations. Too many in our industry tend to hide knowledge because they feel there is too much to lose...designers copying details [first--yes, first to copy], private collectors not allowing pictures because they rent pieces out to movie productions and to brands for copying, or simply fear not knowing what to say when pressed for deeper knowledge. Michael, as demonstrated on this discussion forum and in the book, is fearless and should be commended for that more than anything as that is what contributes to the denim community the most. His humble, yet knowledgeable, way is intensely refreshing.
0 -
On those duck pants. A little detail I hadn't noticed until looking at the pics is the little triangle yoke-ish stitching at the top rear, just beneath the suspender buttons.
It is the yoke. Gives the back better fit and shape. It is especially necessary on stiff fabric that without yoke or darts would look unflattering but more importantly feel uncomfortable and awkward on a moving body.
0 -
In addition to Chocosphere I also recommend Seventy Percent's forum. It's a bit like Superfuture for cacao heads. Even has a section for chocolate professionals. http://old.seventypercent.com/forum/
I also check out Chocolate Alchemy forum from time to time since they break down the forum by process (beans, roasting, cleaning, conching).
0 -
seamless is unique to some, but..
seamless means no train-tracks and leg-twisting:(
This seamless denim is not sanforized...it will twist and shrink a lot.
don't remember how the upper side seams are constructed but if the raw edges are tightly overlocked and busted open and ironed down you'll still get some kind of train track.
What seamless does mean is no selvage edge even though its woven on selvage looms.
Paul- hope you are well.
0 -
Tube tees are actually knit, not woven, on circular knitting machines which generally create cloth by looping yarns. Different yarn insertion method from shuttle weaving looms.
If anything tube denim is probably more similar to double faced fabric in principal.
So it's woven like some t-shirts are woven? Shit looks nice man. Still don't know if I like the fit. The fit on that dude doesn't look so good, but that shirt looks pretty nice.0 -
the jean has seams but it's made with denim that was woven as a narrow tube. So part of the leg is seamless tube. Here are some old pics: http://denimnews.blogspot.com/2008/07/amoskeag-xx-amoskeag-manufacturing.html
Doing this on a shuttle loom that normallly weaves denim requires some serious modifications (additional harnesses that may need to move independently). The easier way would be to get an old loom already configured to weave seamless (aka "pillow tubing") fabrics but that requires a hefty investment.
0 -
This Fashion Incubator post by Kathleen Fasanella will add some dimension to discussions here: http://www.fashion-incubator.com/archive/pop-quiz-denim-quality-pt-2/
copy and paste:
Pop Quiz: Denim Quality pt. 2
Posted by Kathleen Fasanella on Nov 11, 2009 at 3:28 pm / Pop Quiz, Quality / Trackback
I just realized I didn’t make an official-like announcement of the answer to the denim pop quiz last week. I did mention it in the denim laundry contractor posts (pt one, pt two) but not everyone may have seen it. For the record, the darker denim is Japanese. The contractor I interviewed thought it was better quality.
However, I wasn’t satisfied with the frame of the debate. It seemed this quality pronouncement was a matter of fashion, not fact. No one definitively explained the superiority of the Japanese goods. All anyone mentioned were preference factors, differences in weight, finish, and to some extent dyeing. A better comparison weighs characteristics across the gamut of consumer expectations for quality, price and performance. I just can’t see a cowboy working a ranch in those high dollar Japanese denims. On that scale, the latter is inferior quality. This is why I say pronouncing the Japanese denim as higher quality seemed like a value (fashion) judgment rather than a precise qualitative (fact) one.
So, knowing me as you do, I had to ask some textile engineers and manufacturers for their opinions. While all the responses I received said much as I expected, the most succinct, complete and even humorous and surprising response came from consultant John Strickland (resume, pdf), reprinted in its entirety below:
——————-
First off let me get my biases on the table. As a general rule merchandisers, designers, and stylists at the denim labels don’t know the technical aspects of fabric, constructions, or dye shades. They usually muck it up pretty good. There are a few exceptions out there but they are few and far between. For years I have heard this group spout about “x†denim being the best. Early on it was Japanese, later Italian, and now Turkish. They seem to forget all the foreign makers learned their craft from the Americans. So now you know where I stand. For many of my years at Cone Denim I was one of two who taught “Denim 101″ where we brought in customers -usually merchandisers, designers, and stylists- to educate them on the history and the technical details of denim; stuff they need to know.
Denim comes in wide array of qualities to fit the price points needed for the target market. You can divide the fabric groupings into as many slices as you want but generally you can split it into three groups.
1. The $18 to $25 jean for the mass retailers is made on coarse reeds (fewer ends per inch) with coarse warp and fill yarns. The yarns are open end and are not as strong and not as soft but it fits the market. Some might call this denim crap but for a $20 jean it serves it purpose. If anyone tries to make an expensive jean out of this, more power to them. It just will not meet expectations for construction, hand, wash, etc. It is commodity denim.
2. I like to think of the second group as the jeans that fall into the $35 to $100 range at the major brands. These are more highly constructed on a tighter reed and are made from finer yarns. The low end of this range can be open end yarn in both warp and fill and the high end of this range will be ring spun yarns in both warp in fill. In between will be fabrics with ring spun warp and open end fill. Most of the stretch fabrics fall into this category as well. I will not go into it here but you need to have knowledge of denim history and how it changed from work wear to fashion to appreciate what is being done in this category. The gold standard that the denim eroticas aspire to is the old narrow fly shuttle loom fabrics with the woven selvage made up until the 1970’s that has all the flaws and character that everyone wants. The fabrics in this category use the old fly shuttle fabrics for inspiration. They are not the same but look really good anyway. The fabrics are woven on wide high speed looms. The yarns, both open end and ring spun, have computer generated slubs to give the look of the poor quality uneven yarns from the old days. The dye shades are more sophisticated/complicated and allow for some great looking washes.
3. The last group is denim made for jeans that cost more than $100. This is where the denim eroticas hang out. These fabrics will have ring spun yarns in both the warp and fill. These will include the better fabrics from the second group made on wide high speed looms AND the old narrow fly shuttle fabrics made on the old Draper X2 and X3 looms. Cone Denim still has a group of X3 looms making the narrow fly shuttle selvage fabrics. This is what the Japanese have tried to copy. There is a myth that the Japanese bought up all the American fly shuttle looms making denim as they were replaced with new technology. Not true. The Japanese loom makers tried to match the Draper loom and came close but did not get it exact. The American mills make the best denim in the world but there is no doubt that the Japanese, Italians, and Turks have done a great job in catching up.
So to return to your comments, I have to say there is no inherent superiority in Japanese, Italian, or Turkish denim. It does boil down to preference in weight, finish, and dye shade (and I will add construction to this). There are thousands of choices to pick from and matching a desired end look to the appropriate style and shade of denim to provide that desired end look can be a daunting task. It is hard to make a commodity denim look like a high end denim but it fairly easy to take a high end denim and make it look like commodity if you don’t know what you are doing.
0 -
The seamless denim is apparently very difficult to weave (I can imagine why) and likely won't be remade. I heard they actually broke a loom making this yardage. Kenji is a mill fanatic through and through. In fact he has a new, more moderately priced jean called Mill Worker.
As I have long dreamed of producing a jean called Loomfixer (one of the highest paid and most respectable floor positions in the mills of old) I very much respect his work.
I can see the seamless denim is also a mill romantic's homage to the seamless bags woven on old shuttle looms. I am very happy he made it and wish Amoskeag XX much success.
0 -
The yellow from your soak is not indigo. Mostly starch and other slashing and finishing chemicals.
about a year or so ago, kiya posted a link to youtube of the denim dyeing process. shoulda bookmarked it, because i can't find it... maybe he'll re-post.anyhow, i was surprised to learn indigo is yellow until it hits oxygen. really strange seeing the denim go in this yellow vat and slowly get lifted out blue...
when i soak a truly disgusting pair, i look at all the yellow and comfort myself, "it's not accumulated filth, it's just the indigo. you're alright."
0 -
There is a live stream of their shop right now...a band is fiddling and banjoing http://www.ustream.tv/channel/bourbon-blues
0 -
Don't forget his talented wife and partner Sarah. She deserves equal credit. Erk- did you meet their pattern maker? I think she may have been involved with Levi's in the 60's. I am dying to ask her if she worked on the project to switch the 501 to bartacks...the now famous '66
0 -
Come to think of it I remember this jean has felled inseams. Could it be this jean has no visible overlocking? What about where the pocket facing attaches to the pocketing?
0 -
Interesting side seam construction. Looks like the pocket facing is selvage and it's tucked under the front panel's selvage? Is that because you wanted the sides to curve slightly but still have selvage run all the way up to the waistband?
And especially because you did not want to use overlock to attach the pkt facing with the panel there will definitely be a point where the two selvages overlap. The selvage is stopped at a point so it is not double layered when it hits the waistband.
0 -
From my humble blog www.loomchatter.com
The Billiken Man jeans is a beautifully constructed garment. Everything from the beltloops to the button fly facing to the waistband are on point and super playful. The people behind the brand are obsessed with sewing details and offer the mind boggling "triangle" or "three point" overlock stitches (updated, not chainstitches) found on the leg seams, pocketing, and throughout the jeans. As they put it the goal was the "recreation of interlock sewing machines to produce the union special stitches which was considered impossible before." Did they hack their sewing machines?
In line with many Japanese business and craftsman practices they took two American icons, the Billiken Man and jeans, and applied such unique twists and enhancements that the end result is something that reflects pure Japanese artistry. And obsession.
If you have not heard of the Billiken Man you are probably not alone. A quick Google search shows that it was once a popular American pop culture icon that even had popular songs singing its praise. The original Billiken was designed by artist Florence Pretz as a symbol that evoked good luck. Pretz allegedly saw the figure in a dream who told her that good luck can be had by rubbing his feet. It is further believed that Billiken is the namesake of President William Howard Taft. The "ken" part of Billiken is likely a bastardization of the word Can in "Billy Can" as in there are those Billys who can and those Billys who can't. Billiken then is obviously meant to inspire the "can do" attitude that helps a nation get through difficult times.
The Billiken license was eventually picked up by Horsman Dolls, Inc., the American toy company that marketed the Teddy Bear named after President Theodore Roosevelt. Today the Japanese have incorporated the Billiken man into their cast of deities. If you visit the Tsutenkaku tower in Osaka you will find a statue of the Billiken enshrined there.
The makers of these jeans have invoked the good spirit of Billiken to create a jean full of playful details. The orange thread used throughout the jeans are reminiscent of Billiken's hair color and the wavy back pocket stitching reflects the overall features of the smiling, seated character. The company proclaims the jeans "will assure you of the lively and optimistic lifestyles in this challenging moment in our history."
The stitching that appears to be a bartack is actually a zigzag stitch.
If you are ever in need of a shot of luck just rub the Billiken Man's feet wherever you are.
The button holes are beautifully executed with a hand-tied-tail look and a stitch that changes pitch towards the curve.
Billiken Man Website
0 -
I've always liked Erwin and Stifel
0 -
Amoskeag and Cone denim were quite different denim; principall, Amoskeag was natural indigo, Cone was synthetic. Amoskeag fanric has a green cast, Cone a red cast. The first Cone denim is very dark; they were still hand dye-ing it in vats, so there was continuous variaiton in the early days of their, too. I don't think the wieghts differed; between 1915 and 1922 the 501 was being made with denim from both places, so I guess the weight was the same.
Some of the COne denim Levi's from the 20s are REALLY dark. Where most of the Amoskeag ones from the 1910s fade in a very different way, fewer whiskers, more thigh wear. Hard to know how much of this is due t o natural v synthetic, and how much is other factors.
If you haven't seen this Cone story, it's worth looking at. A lot of technical stuff.
You are very knowlegable!
There is still no solid evidence whether Cone was exclusively using natural or synthetic indigo during the period in question, 1900 -1920. Certainly when Proximity started in 1896 it would have used natural indigo particularly because synthetic indigo did not become profitably commercially marketed and available until at least 1897. There is also the question of whether Cone would have used synthetic indigo during World War I. Was there a non-German source for synthesized indigo at this time?
0 -
me too, got to check if it is already available at burg &schild
The shirt is no longer available. Think it was really limited. He's making more in chambray. You can call his shop. He was taking names the last time I spoke with him.
0 -
Don't know why but saw this on my feed for the Rising Sun blog and instantly thought of Superfuture:
0 -
Just got back from throwing darts and drinking local Greensboro beer with Sarah and Victor. Their enthusiasm is inspiring.
They not only cut and sew their production orders in their workshop but they really know what they are doing. It is one thing to have factory drones do all the dirty work and quite another to execute every step from design to final product with your own hands. This way of working is extremely rare today and requires immense talent and energy.
They currently produce a fantastic fashion product, although Victor does have a purist side. I like to think of their approach to denim sewing as being similar to what Wiley Dufresne does in his WD-50 restaurant. They are master nerds of their respective subjects and are not afraid to play and experiment. If you look at their jeans with a careful eye you will see details that make you question how they were sewn. In a way they are engaging people to be curious and study an uncommon seam construction, let's say.
I look forward to seeing the "ubergeek jean" (Sarah's words) they recently designed. It is supposed to be a seemingly basic 5-pocket jean with easter egg details. You can expect great things from these two.
Oh all the chainstitched hems are done on vintage Union Specials. They also have a pretty decent button hole machine.
0
Jeans of the Old West: A History
in superdenim
Posted
The yarns used is more a matter of choice but due to comfort you normally would not make clothing with heavy canvas. It does not drape as well as twill weaves and from experience the many warp/weft crossings are not conducive to comfort against the skin. That is why most plain weave fabrics for clothing tend to be more fine (finer yarns).
Canvas also tends to crease more easily than twills. Plain weave is the least wrinkle-resistant of all weaves (your whiskers and honeycombs would be gorgeous on indigo canvas). With workwear that is not washed often one would imagine that over time the fabric would experience yarn breakage more often than the more drapey twill. But don't be mistaken. Given the same yarns of same quality cotton, pound for pound, canvas generally stronger than 3x1 twill.